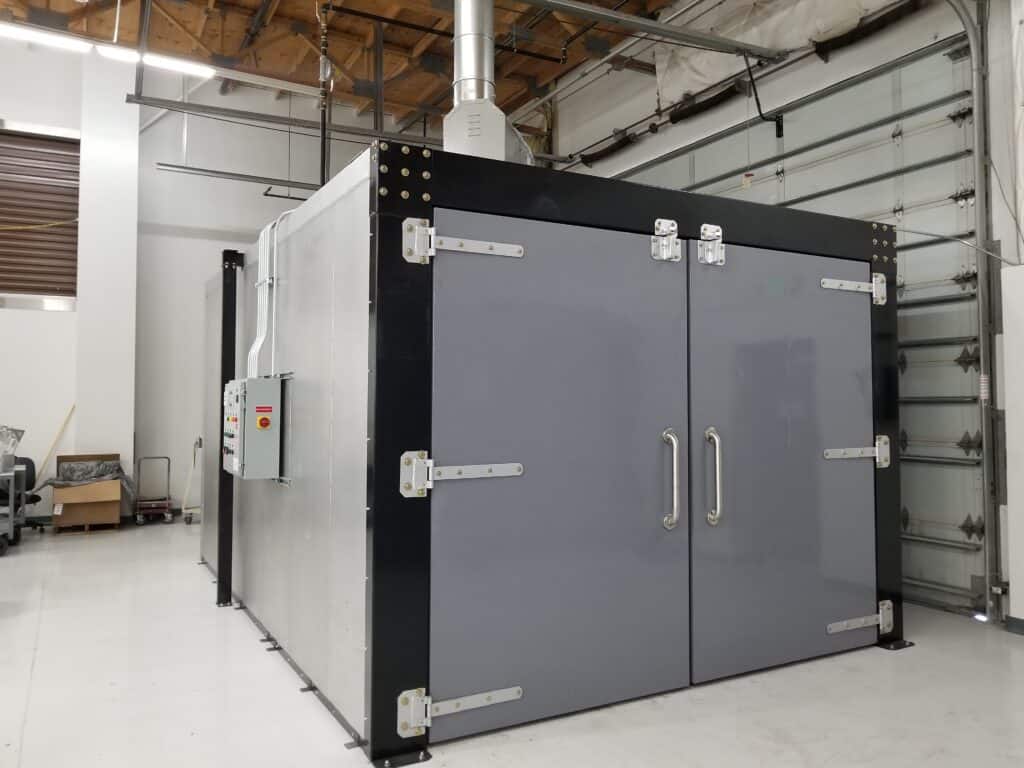
Powder coating requires precision, and the right curing oven makes all the difference. A 6’ x 6’ x 10’ powder coating oven provides the perfect balance of size, efficiency, and performance for rims and small parts. With its controlled heat distribution and optimized airflow, this oven guarantees a flawless finish every time.
Perfect Heat Distribution Ensures Every Rim and Small Part Cures Evenly
Consistent heat is essential in powder coating, as uneven temperatures can lead to flaws in the finish. This powder coating oven is designed to distribute heat evenly across its 6’ T x 6′ W x 10′ L interior, ensuring that every inch of a rim or small part receives the right amount of curing. Without uniform heating, powder particles may not bond properly, leading to an inconsistent coating or weak adhesion.
With a 750,000 BTU/HR maximum output and recirculating airflow of 7,000 CFM+, heat moves efficiently throughout the chamber, eliminating cold spots that could affect curing. By maintaining an even temperature across all surfaces, this oven prevents over-curing or under-curing, which can weaken the final finish. The well-balanced heat system ensures that every part—no matter where it’s positioned—comes out with a flawless, durable coat.
Compact Size Minimizes Heat Loss, Keeping Curing Times Consistent
Larger ovens often struggle with heat retention, requiring longer warm-up times and excessive energy use. This 6’ x 6’ x 10’ oven is compact yet spacious enough for multiple rims and small parts, keeping heat contained for efficient curing. The 6” thick insulated walls, roof, and doors ensure that internal temperatures stay steady, reducing fluctuations that could impact the coating process.
Because less heat escapes, the oven reaches curing temperatures faster and maintains them with minimal energy loss. This consistency results in more predictable curing times, preventing delays in production. Whether coating a batch of small parts or a set of rims, users can rely on this powder coating oven to provide steady performance without unnecessary downtime.
Optimized Airflow Prevents Uneven Coating and Patchy Finishes
Airflow plays a critical role in the powder coating process. Poor circulation can create uneven coatings, causing some areas to cure properly while others remain underexposed. This oven’s 7,000+ CFM recirculation airflow system eliminates that risk by keeping heated air in constant motion, ensuring every surface of a part cures uniformly.
With a well-balanced airflow system, powder melts and bonds evenly, reducing the chances of drips, sags, or missed spots. The strategic airflow design also helps maintain temperature stability, making it easier to achieve professional-quality finishes without inconsistencies. For rims and small parts, this level of control is essential in producing high-quality, durable coatings.
Precision Temperature Control Avoids Overheating or Under-curing
Achieving the ideal curing temperature is essential for a strong, durable powder coat. Too much heat can burn or discolor the finish, while too little heat prevents the powder from bonding correctly. This oven’s precision temperature controls ensure that heat remains within the required range, preventing costly errors.
The 6# density mineral wool insulation maintains stable internal conditions, while the aluminized or G90 galvanized prime U.S. steel construction enhances durability and heat retention. With precise regulation, rims and small parts receive the exact amount of heat needed for full curing, eliminating the risk of brittle finishes or premature coating failure.
Space-efficient Design Allows for Multiple Parts to Cure at Once Without Crowding
Maximizing oven space without compromising airflow is crucial for batch processing. This 6’ x 6’ x 10’ interior provides enough room to cure multiple rims and small parts simultaneously, increasing efficiency without overcrowding. Proper spacing within the oven allows heat and air to circulate freely, ensuring that every part receives uniform curing.
Because this powder coating oven is designed to handle multiple items efficiently, operators can coat and cure more parts in a shorter time frame. This feature is especially beneficial for businesses handling high-volume production, as it reduces bottlenecks while maintaining high-quality results.
Faster Heat-up Times Mean Quicker Turnaround for High-volume Jobs
Downtime can be costly in any powder coating operation. A slow-heating oven can delay production and create scheduling challenges. This oven’s high-efficiency heat system reaches curing temperatures quickly, allowing operators to move from coating to curing without unnecessary waiting.
By minimizing heat-up times, this oven speeds up the entire powder coating process, making it ideal for businesses handling frequent jobs. Faster curing cycles lead to higher productivity, helping to meet tight deadlines while maintaining top-tier finishes. Whether working on custom projects or large orders, this oven ensures a steady workflow with minimal interruptions.
Insulated Walls Maintain Steady Temperatures for Flawless Powder Adhesion
Temperature fluctuations can weaken powder adhesion, leading to peeling, chipping, or inconsistent finishes. This oven’s 6-inch thick insulated walls, roof, and doors prevent heat loss, keeping internal temperatures stable throughout the curing process. The 6# density mineral wool insulation enhances thermal efficiency, ensuring the oven maintains optimal curing conditions.
Steady temperatures allow the powder to fully bond with the surface, creating a durable, long-lasting finish. Whether curing rims or small parts, this insulation design ensures that every coated piece meets professional standards. Consistency in curing translates to fewer reworks, better durability, and a higher-quality final product.